Buildings constructed using low embodied carbon and sustainable materials are crucial for the environment
By: Yip Wai Fong
There is more than meets the eyes when we gaze at the skyscrapers dotting the city’s skylines. Each of them is a carbon funnel, releasing CO₂ to the atmosphere before and during construction, and during its operational lifespan. According to the International Energy Agency, buildings worldwide account for 39% of energy and process-related CO₂ emissions in 2018, with as much as 11% of it the results of building material manufacturing such as steel, cement and glass.
But as sinking coastlines threaten to bring buildings tumbling down with it, a wave of transformation has been sweeping over the building industry. Growing environmental awareness as well as the government’s encouragement has spawned buildings constructed in part using low embodied-carbon (EC) materials and energy-efficient products. The inclusion of sustainable building materials also forms many Green Building rating tools, such as Malaysia’s Green Building Index, GreenRE and MyCREST.
“Examples of environmentally friendly building materials which are available in the local market include bamboo, recycled metal, reclaimed wood, low VOC paints etc. These materials are considered green due to their sustainable sourcing, reduced carbon footprint, and minimal negative impact on the environment. Bamboo grows quickly and requires minimal resources, while recycled metal and reclaimed wood decrease the demand for new resource extraction. Low VOC paints emit fewer harmful chemicals, improving indoor air quality. These materials conserve natural resources, promote responsible consumption, and contribute to a more sustainable construction industry in Malaysia,” said Arkitek Leong PL principal and Malaysian Institute of Architects (PAM) past deputy president Alice Leong.
Royal Institution of Surveyors Malaysia immediate past president Dainna Baharuddin said green building materials can be identified by eco-label certifications. It includes major construction materials such as cement produced with recycled materials (green cement), Industrialised Building Systems (IBS), as well as non-major construction materials that are energy conserving such as lightbulbs and high-efficiency toilets (dual flush cistern), and durable, low maintenance and long-lasting building materials such as high-density polyethene (HDPE) based materials in the form of tank, pipe, infrastructure and drainage system.
“Initiatives by the government as well as promotion by non-governmental organisations and education institutions have made people not only more responsible towards the environment but also conscious about building sustainable projects and developments in Malaysia,” said Dainna.
“Products such as high-density polyethene for pipes, lightweight blocks, gypsum board, low VOC paint, energy saving lightbulbs and high-efficiency toilets are widely used (but) IBS, Low-Emissivity (Low-E) glass and other specialist systems would depend on the project owner’s budget and the purpose of a particular building project,” she added.
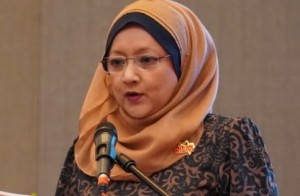
The higher initial cost for using sustainable materials in developments is balanced out by saving in the long run due to lower maintenance and lower energy use, said Dainna.
Cost is a barrier
Perception about the high cost of low EC materials is one of the major barriers preventing more widespread usage in Malaysia. A study on greenhouse gas (GHG) emissions by the Construction Industry Development Board (CIDB) in 2020 found that low carbon materials tend not to be considered as consumers’ first choice during the planning and preparation of project bill of quantities due to the perception of the materials’ high cost.
“The range and variety of certified green building materials are still limited in the market which contributes to higher material cost (of) building sustainable projects and developments in Malaysia,” said Dainna. “However, the higher initial investment would be saved by the running costs due to reduced energy consumption and lower maintenance. It would also assist in reducing carbon footprint in the environment.”
Concurring with Dainna, Leong said that although using these materials incurs higher costs, the building industry’s receptiveness to them is steadily growing.
“Some eco-friendly materials might have higher upfront costs, (but) they often yield long-term savings through reduced energy consumption and maintenance expenses. Many companies prioritise sustainable practices as part of their corporate policies or social responsibility efforts, (which) influence the adoption of green building materials, (and) more collaboration among the building industry associations, educational institutions, and advocacy groups to raise awareness about the benefits of environmentally friendly materials is fostering a culture of sustainability,” she said.
“However, challenges remain, such as resistance to change, lack of awareness, and concerns about initial costs (so) the promotion, education, etc. must be carried on,” she added.
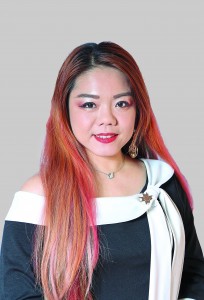
Receptiveness towards using green construction materials is steadily growing in the industry, said Leong.
On-going efforts to involve more stakeholders are being undertaken by the Construction Research Institute of Malaysia (Cream), a CIDB subsidiary. Recently, Cream and YTL Cement have signed an MOU for a collaboration. YTL Cement is one of the earliest local green cement manufacturers and has recently launched its ECO brand of green cement, green concrete, green mortars and engineered sand.
Cream Construction Industry Consultancy manager Mohd Khairolden Ghani explains that the collaborations cover personnel development, research and development (R&D), and support for the transition to sustainable construction.
“CIDB and YTL Cement will be jointly designing training programs and training syllabi for accreditation programmes of qualified personnel in operations. It is hoped that this will assist in attracting, retaining, and growing skilled workers and experts in the construction industry.
(Secondly), YTL Cement is offering access to its laboratory and testing facilities. Cream will work with YTL Cement’s team of experts to conduct R&D on lower embodied carbon alternatives in materials and construction methods.
(Also), YTL and Cream will be developing a Sustainable Construction Roadmap that outlines the steps, goals, and actions necessary to integrate environmentally, socially, and economically responsible practices into construction projects. We are predicting the Roadmap (to) be ready early next year,” Khairolden explains.
One of the major recommendations in the CIDB study in 2020 is to focus on reducing emissions by the five highest GHG contributors among construction materials namely ready mixed concrete, steel reinforcement, bricks, cement finishes and metal. While agreeing that it is high time for the construction industry to adopt green cement, Khairolden said that it, as well as the broader sustainable practices, requires collaboration among government agencies, construction companies, researchers, and the wider construction industry.
“(Due to the) multifaceted nature of (sustainable practices), collaboration of various stakeholders is essential because sustainable construction practices are not isolated efforts, they require systemic changes across industries, technologies, regulations, and societal attitudes. The complexity of these changes necessitates a collective and coordinated approach to achieve meaningful and lasting results in the built environment,” he said.
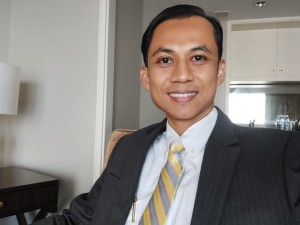
Implementing green building materials and sustainable practices in the industry requires multi-party collaboration, said Khairolden.
Stay ahead of the crowd and enjoy fresh insights on real estate, property development, and lifestyle trends when you subscribe to our newsletter and follow us on social media.