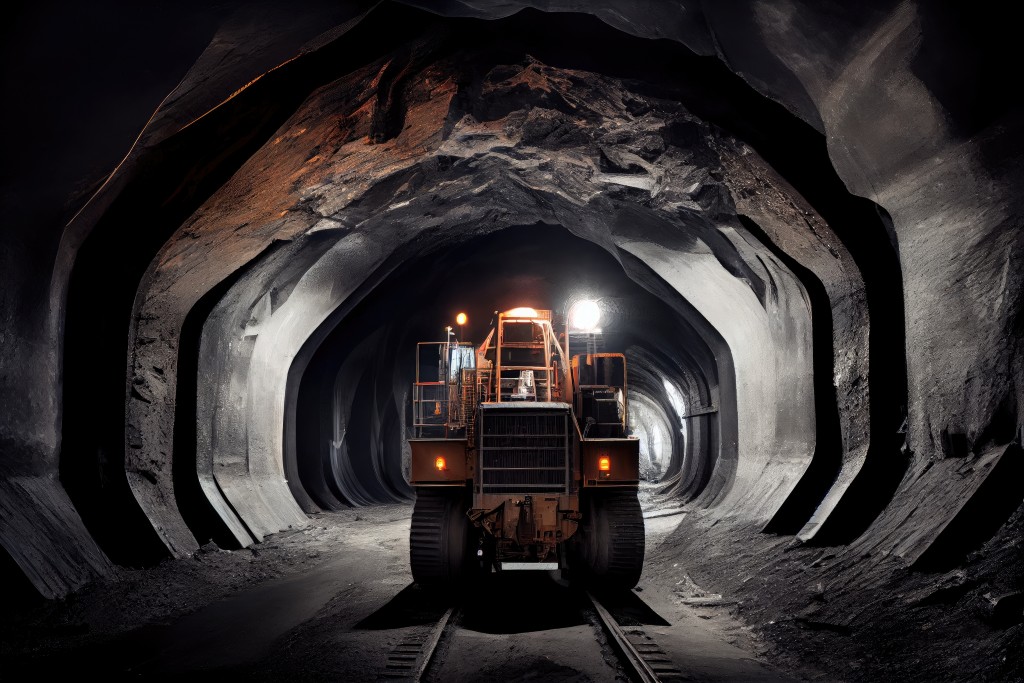
The extreme dangers include cave-ins and falling debris but there is also the concern of human limitations.
The infrastructure landscape in Malaysia has seen a transformation. The East Coast Rail Link (ECRL) and the proposed Kuala Lumpur-Singapore High-Speed Rail (KL-SG HSR) are some mega projects displaying a testament to Malaysia’s desire to advance into a high-income and well-connected economy. However, such projects have seen more ventures into the underground, which are constantly rife with safety hazards and blockages leading to frustration and inefficiencies. That is why recently with the help of artificial intelligence (AI), automation has revolutionised underground construction in Malaysia.
Before automation, manual labour was the way forward as a conventional method for tunnel boring and excavation. The extreme dangers include cave-ins and falling debris but there is also the concern of human limitations. Overworked and fatigued workers will ultimately lead to extended project timelines, and that is why automation offers a compelling solution.
Mechanised moles
When it comes to the underground, a big metal drill always comes to mind. Tunnel Boring Machines (TBMs) are incomprehensibly colossal and carve easily through rock and soil. They are equipped with intelligent sensors and navigation systems to reduce the risks of incorrect tunnelling against other structures while also minimising the need for human intervention. While at a significant cost to operate, TBMs can run for a long time which accelerates project completion times faster than any human could. But even then, complications can happen.
For example, MMC-Gamuda Sdn Bhd, a joint venture between MMC Corporation Bhd and Gamuda Bhd encountered an issue where karstic limestone conditions disrupted the progress of drilling the Stormwater Management and Road Tunnel (SMART) project years ago. Numerous sinkholes opened as a result, significantly damaging public roads and properties. As a result, a TBM with a variable density (VD) enhancement was developed and incorporated into another project, the MRT Kajang Line. The enhancement resulted in a 95% reduction in sinkhole occurrence compared to the SMART project. It is now continuously being optimised and has led to the debut of the autonomous VD TBM for the MRT Sungai Buloh-Serdang-Putrajaya (SSP) line.
Safety is paramount
Construction dust is a term everyone is familiar with, not just engineers and construction workers. It is already hazardous drifting around above ground, so what about the workers below? The benefits of automating such dangerous processes minimise human exposure to toxic gas inhalations and other dangers. Additionally if set up correctly, environmental disruptions are reduced as well due to the controlled nature.
In this case, environmental data is necessary. The tunnel network is equipped with sensors that are embedded throughout to continuously monitor critical parameters such as air quality, ground pressure and structural integrity. By feeding this real-time data into a central control system, engineers are able to anticipate problems and take proactive measures to resolve them. It becomes possible to perform predictive maintenance, which stops equipment breakdowns and guarantees efficient tunnel operations.
High upfront costs
If automating the construction industry was that easy, Malaysia would already be overrun with robots. Unfortunately, that dream needs its plug pulled because the initial investment to acquire and utilise such sophisticated equipment can be a real tear-jerker. Not only that, the integrating process of these new technologies into current workflows requires careful planning that Malaysia may not exactly be ready for yet.
Thinking long-term though, the benefits outweigh the pain. First and foremost is the subsequent safety for workers, which for Malaysia currently is not at its best. There will also be improved project efficiency and the freedom to explore more complicated tunnelling systems that were previously impossible. The best of all is that automation will enhance Malaysia’s global competitiveness, attracting international investment projects and driving economic growth.
Governmental support
Collaboration between different stakeholders is necessary to fully realise the potential of automation. By offering incentives to developers to adopt new technologies, the government can spur the construction industry further. At the South East Asian Conference and Exhibition in Tunnelling and Underground Space (Seacetus 2024) in Kuala Lumpur (KL) on May 5, Works Minister Datuk Seri Alexander Nanta Linggi stated the Works Ministry is committed to supporting Malaysia's construction transformation into a high-tech one. It would also be in line with the 12th Malaysia Plan (2021–2025) which emphasises that the policy aims to expedite the adoption of cutting-edge technologies. This strategic integration of AI and automation is aligned with the Fourth Industrial Revolution’s goals to boost the nation’s digital economy.
Leaders in the industry must, in turn, make investments in research and development (R&D) to expand the realm of what is feasible. The workforce also needs to be prepared for the shifting environment of educational institutions.
Looking ahead, automation will definitely play a role in Malaysian underground construction. These cutting-edge solutions provide a way to improve safety, efficiency, and sustainability as the country launches large-scale infrastructure projects. By adopting automation, Malaysia can protect its workers, accelerate project completion and move closer to an intelligent, controlled and environmentally conscious future for infrastructure development. This technological revolution will create the foundation for a stronger and more connected Malaysia in addition to revolutionising the construction industry.
Stay ahead of the crowd and enjoy fresh insights on real estate, property development and lifestyle trends when you subscribe to our newsletter and follow us on social media.